With years of project experience in clean production, wastewater treatment, and resource recovery within the electroplating and surface treatment industries, our technical team has developed a series of effective and cost-efficient solutions to address the challenges of heavy metal wastewater. These challenges include the diverse and complex nature of the wastewater, difficulty in meeting discharge standards, high chemical dosing requirements, the risk of biological toxicity, and the high costs of reclaimed water reuse. We provide comprehensive technical services for ultra-pure discharge, sludge reduction and harmless treatment, reclaimed water reuse, and heavy metal resource recovery.
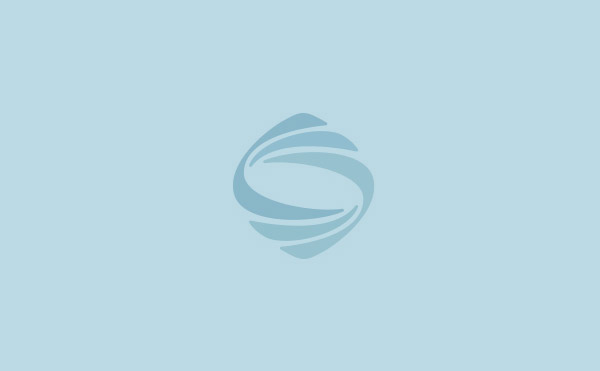
Ultra-Pure Discharge Process
For heavy metals with complex forms and poor sedimentation properties, we employ catalytic oxidation to break down complexes, high-molecular polymers for co-precipitation, specialized ion-exchange resins, and membrane separation technologies. These processes ensure stable compliance with the discharge standards outlined in the Electroplating Pollutant Discharge Standards (GB 21900-2008), meeting at least Table 2 standards and, in some cases, even Table 3.
Technical Features
The complexation process can be performed with little to no introduction of salts.
Our proprietary chelating agents are efficient, fast-acting, and compatible with subsequent membrane treatment.
Membrane separation is used for the deep removal of particulate heavy metals from wastewater, preventing the re-dissolution of these particulate metals.
Special ion-exchange resins offer high treatment and regenerable capacity.
The process combination is flexibly adjusted based on water quality to achieve ultra-pure discharge.
Our proprietary chelating agents are efficient, fast-acting, and compatible with subsequent membrane treatment.
Membrane separation is used for the deep removal of particulate heavy metals from wastewater, preventing the re-dissolution of these particulate metals.
Special ion-exchange resins offer high treatment and regenerable capacity.
The process combination is flexibly adjusted based on water quality to achieve ultra-pure discharge.
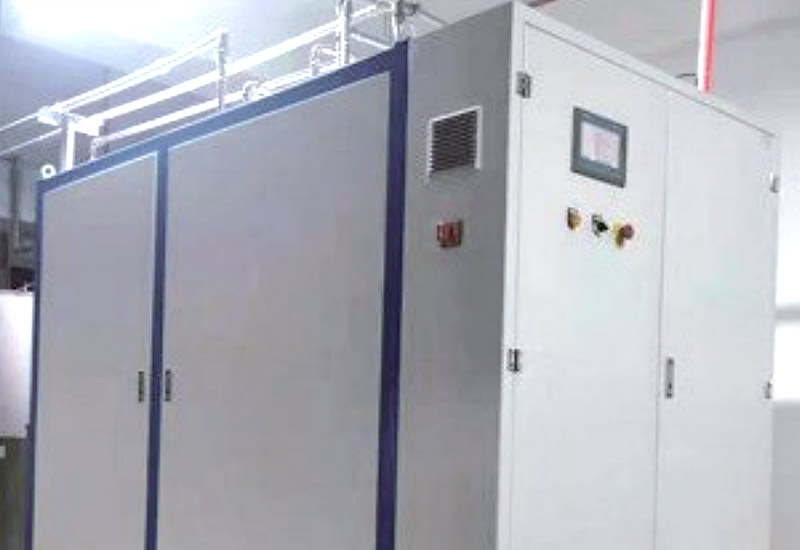
Heavy Metal Sludge Resource Recycling Process
Heavy metal wastewater is treated through coagulation and sedimentation to produce heavy metal sludge. After efficient pressure filtration and drying, the sludge moisture content is significantly reduced, achieving substantial volume reduction.
Technical Features
? Solid content of the sludge up to 80%, with a significant reduction in volume.
? No or minimal flocculants are used, enabling the resource recycling of heavy metal sludge.
? No or minimal flocculants are used, enabling the resource recycling of heavy metal sludge.
Electrolytic Recovery of Heavy Metals
Under the influence of an electric field, ion exchange membranes are used to divide the electrolytic cell into cathode and anode chambers. Redox reactions occur at the electrodes, and by automatically controlling parameters such as pH, current, voltage, and ORP, valuable metal resources are recovered at the cathode. This process is particularly effective for high-concentration heavy metal wastewater, such as copper etching solutions, high-concentration tank liquids from production lines, and concentrates from water reuse systems.
Technical Features
With low labor intensity, high automation, and simple operation and maintenance, the system avoids the generation of harmful gases such as chlorine at the electrodes, preventing secondary pollution.
It also enables on-site recovery of water in production lines, with dedicated recovery lines set up within the plant.
The purity of the recovered metals is ≥99.5%, ensuring high recovery value.
It also enables on-site recovery of water in production lines, with dedicated recovery lines set up within the plant.
The purity of the recovered metals is ≥99.5%, ensuring high recovery value.